
OrderManagement
Intelligent sample and order management
By using LAB-OrderManagement, you can integrate electronic laboratory order data from OrderEntry systems, evaluate paper-based laboratory orders, access materials data from loose material sorters and process all the order data globally in a single solution. The result: increasing efficiency with reduced manual processing, together with a significantly faster response to the sender.
The future of order recording in the laboratory
LAB-OrderManagement enables the structured order recording of electronic and paper-based orders in conjunction with materials information via manual sample registration together with loose materials sorters. The module minimises the error rate that occurs due to missing samples or order data, thus speeding up the laboratory organisation's efficiency and quality.
Faster processing of incoming samples
Thanks to automation, the LAB Order Management software enables job registration in the laboratory to take place considerably faster, reduces potential errors caused by manual working steps, and significantly improves response and information times vis-à-vis senders. Simplified familiarisation of new staff with the receipt of specimens is an additional benefit.
Your contact partner
Olaf Hennings
Product consultancy
Tel.: +49 40 727360 79
Collecting/recording order data in the laboratory – quickly and securely by using OrderManagement
Automated and manual sample registration
Maximum speed when recording samples through the integration of automation systems/loose materials sorters together with touchscreen-optimised, manual sample registration points etc. for special materials.
Integrating electronic order data
Interfaces to import electronic laboratory orders from a wide variety of OrderEntry systems – for document-free order processing in the laboratory.
Scanning and recording paper orders
By default, OMR laboratory cards and machine-readable laboratory orders are recognized and processed.
Sample and order management
LAB-OrderManagement is based on the fast separation of sample and order data. Each item of information is individually processed at maximum speed, then undergoes optimum preparation in LAB-OrderManagement for correction or direct export.
Expanded correction in VERIFY with materials data
The merging of data that is still implausible takes place directly in the correction stage. For each order, the required laboratory parameters, the expected material, the registered primary material and its quantity are available here.
Interface grouping during export
Regardless of how many input channels are present from paper orders, OrderEntry and sample data in the laboratory, the LAB-OrderManagement module processes this information and transfers this data to the laboratory system via a central interface.
Features of LAB-OrderManagement
Manual sample registration
The manual sample registration feature of LAB-OrderManagement enables the sample together with the sampling source and pre-analytical notes to be already registered when the sample is received.
After recording the sample number, you cumulatively assign predefined sample types to the order. After sending off the recorded sample list to the order, further processing takes place analogously to the data sets of the electronic sample recording.
Display and correction in the VERIFY module
Display and merging of the data subsequently takes place directly in the VERIFY module. During correction, the following additional data for each order is visible:
- Expected material (determined from the analysis that is requested)
- Primary material registered in the sample distribution
- Number of registered primary materials
Depending on the status between the order and the registered material, the user can decide in VERIFY whether the order:
- is transferred to a special clarification point for further processing if there are discrepancies, so as not to delay the collection/recording routine.
- is exported directly to the LIMS (Laboratory and Information Management System) together with the registered material if all the information is present.
Best practice in medical laboratory
OrderManagement with Mediaform
Modern requirements for order entry in medical laboratories and hospitals have long since gone beyond the scanning and evaluation of paper-based forms. In the context of future-proof digitization, it is essential to cover all disciplines in the area of preanalytics.
The ScanTools software handles the centralized capture, evaluation and control of incoming lab samples, as well as paper-based and electronic lab referrals – one solution for everything. How does this work? We took a closer look at the process at MDI Limbach Berlin.
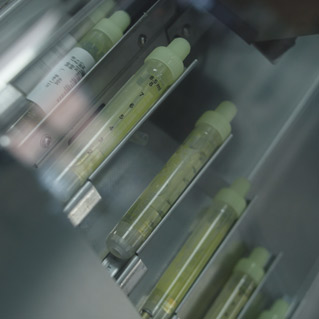
OrderManagement with the software ScanTools
Our customers
